3 Common Causes of Workplace Incidents and How to Avoid Them
Occupational hazards are present in all workplaces, and it is important for organisations to mitigate these risks through the adoption of strict safety protocols. By identifying potential pitfalls and implementing robust safety measures, companies can create safer work environments and uphold the well-being of their employees while ensuring the continuity of their operations.
Occupational hazards are present in all workplaces, and it is important for organisations to mitigate these risks through the adoption of strict safety protocols. However, in critical industries such as oil and gas and manufacturing, these risks are amplified due to the dangerous and often unpredictable nature of the processes carried out. Incidents in these industries can lead to not only severe injuries but also environmental disasters, production downtimes, and significant financial losses.
Therefore, it is paramount for businesses in these sectors to understand the root causes of workplace incidents in order to develop effective prevention strategies.
In this blog, we will delve into the primary causes of workplace incidents within critical industries and explore proactive measures organisations can take to avoid them. By identifying potential pitfalls and implementing robust safety measures, companies can create safer work environments and uphold the well-being of their employees while ensuring the continuity of their operations.
Common causes of workplace incidents in critical industries
Workplace incidents encompass any occurrence that transpires during the execution of an employee's work responsibilities, culminating in harm or ailment.The spectrum of these incidents spans from minor cuts or bruises to severe injuries, incapacitations, or fatalities.
According to the United Nations of Global Compact (UNGC), each year, an estimated 2.78 million workers die from occupational accidents while an additional 374 million workers suffer from non-fatal occupational accidents. Of these cases, the most common causes were found to be:
- Slips, trips, and falls from height: Within critical industries, where operations often involve working on elevated platforms, scaffolds, or structures, the risk of slips, trips, and falls from height becomes particularly pronounced. The inherent challenges of working in these environments, such as exposure to adverse weather conditions and the necessity for precise footing, significantly amplify the likelihood of such incidents. Whether it's an oil rig, manufacturing facility, or construction site, the potential consequences of these accidents can range from severe injuries to disruption of operations and financial setbacks.
- Struck by moving or falling objects: Employees working in close proximity to cranes, vehicles, or areas where materials are being lifted face an elevated danger of being struck by falling or moving objects.
- Contact with machinery: In settings like manufacturing plants or energy production facilities, the potential for accidents arising from machinery operation, maintenance, or repair is ever-present. Workers who interact with these machines, whether through operation, maintenance, or troubleshooting, face the inherent risk of being caught in moving components or entangled in machinery. The repercussions of such incidents can be dire, resulting in severe injuries, amputations, or even fatalities.
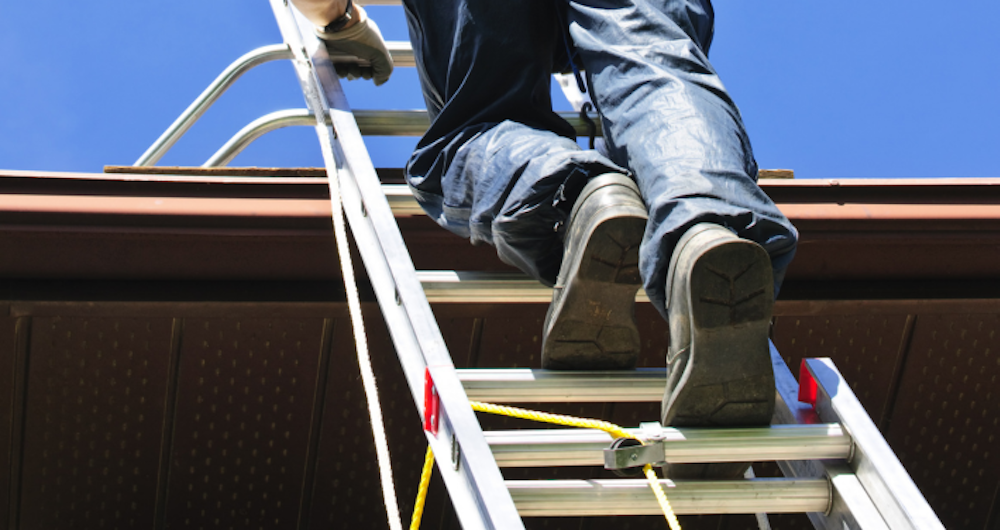
Strategies for avoiding workplace incidents in critical industries
By identifying the risks associated with occupational processes, organisations can effectively implement appropriate preventative safety measures. Let's take a look at some of the strategies employed in high-risk environments to prevent common workplace incidents:
- Drop Prevention Equipment: At onshore and offshore facilities, falling or dropped objects can occur for many reasons, including poor maintenance, harsh weather conditions, moving equipment or even human error. This can be a significant risk if best-practice dropped object procedures are not followed. To avoid dropped object-related accidents from happening, it is important for facilities to have proficient drop-prevention measures in place. This can include the use of drop-prevention mats and nets to catch falling objects, or cable ties to fasten tools and equipment.
- Safety Tagging Systems: In environments such as manufacturing plants and energy production facilities, the likelihood of accidents stemming from machinery operation, maintenance, or repair is constantly prevalent. In conjunction with machinery-related hazards, the use of dangerous equipment such as ladders, scaffolding and motorised tools can also pose significant dangers if not maintained or used properly.
To ensure personnel are kept safe when working with high-risk machinery and equipment, the use of safety tagging systems is essential. These systems introduce an essential layer of accountability and visibility to the operational framework of critical facilities. For example, inspection tags affixed to machinery and equipment, serve as visual indicators of diligent maintenance and readiness for safe usage. By clearly displaying crucial information like inspection dates, maintenance records, and compliance status, these tags ensure workers have real-time insights into the operational status of machinery.
- Safety Signage: One of the most effective ways to alert personnel to potential hazards in the workplace and inform them of best practices, is the implementation of highly visual safety signs. According toHSE, safety signs and signals are required where a “significant risk to the health and safety of employees and others remains”.
There are 4 main types of safety signs used in workplaces, and these include prohibition signs, warning signs, mandatory signs and emergency signs. The presence of these safety signs serves as a constant reminder of the risks inherent in workplaces, reinforcing the significance of adhering to established safety protocols. By fostering a visual culture of safety awareness, organisations can ensure personnel make informed decisions and take responsible actions when carrying out dangerous operations.
In addition to the above safety strategies, it is imperative to underscore the pivotal role that consistent risk assessments and comprehensive safety training play in maintaining a secure workplace environment. Regular risk assessments and staff training stand as a cornerstone of proactive hazard management.
These processes involve the systematic identification, evaluation, and mitigation of potential risks across various operational aspects, and ensure all workers are up to date on the latest safety regulations and laws. By routinely scrutinising the work environment, processes, and equipment, organisations can pinpoint emerging hazards and swiftly implement corrective measures.
Create and maintain a safe work culture with REGALTAG
At REGALTAG, we provide tough workplace safety tagging and signage that meets all safety specifications and needs.
We believe every safety process is unique. That’s why all our solutions are completely customisable so you can ensure they’ll be most effective for you. Our designers can guide you through with up-to-date knowledge of industry best practices and thousands of tried and tested existing signs for inspiration.
The durability of your signs and tags is also important so that they always remain intact to carry out their important role. We provide a range of durable safety solutions fit for any conditions.
In our range of safety signs, and tags we offer:
- UV and fade resistance
- Freeze-proof
- Lightweight options
- 100% recyclable materials
- Scratch- and scuff-resistance
- Customisable
If you’d like to find out more about how we can help with your safety processes, contact our friendly team at REGALTAG® today. We’re more than happy to answer any questions you have and can guide you through each material option.
Subscribe
Join 10,000+ others receiving our monthly updates. Free Tag knowledge delivered straight to your inbox.